Реверс-инжиниринг изделий из пластмасс: мифы и реальность
Обратный инжиниринг (реверс-инжиниринг) — это распространенный метод разработки и постановки на производство изделий из пластмасс. Особенную популярность эта технология приобрела в последние годы в условиях санкционного давления и изменения логистических цепочек поставок большого ассортимента изделий. Обратный инжиниринг предполагает довольно простой алгоритм действий и быстрый результат, что может ввести в заблуждение заказчиков, не являющихся специалистами в физике полимеров. Ниже приведены основные мифы, укоренившиеся в данной сфере, причины их распространенности, а также реальные ситуации в области разработки изделий из пластмасс таким способом
Для исследования химического состава полимерной композиции применяется большой ассортимент аналитических методов, каждый из которых имеет свою область применения и свои ограничения, которые приведены в табл. 1.
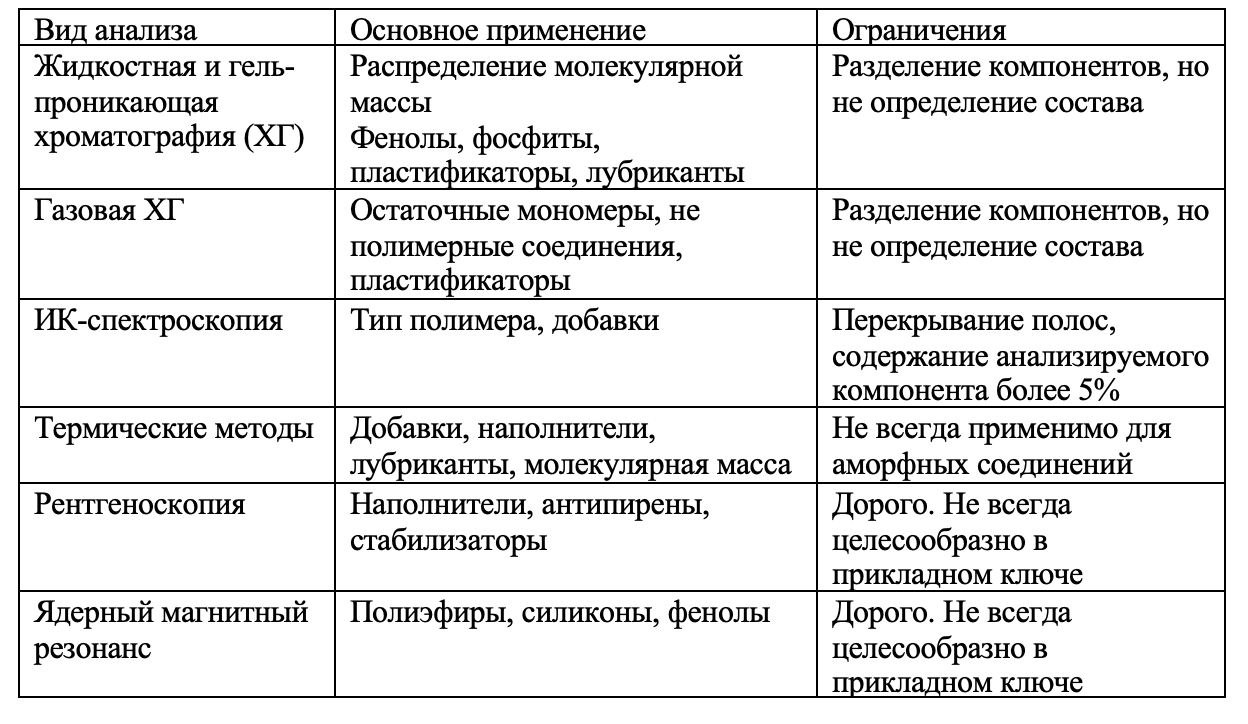
Самым важным ограничением в наборе аналитических методов является невозможность определения конкретной марки и, тем более, производителя полимерного компонента или добавки.
Так, например, для разных по качеству меловых добавок объем ввода в полимер будет разным. Качественная меловая добавка должна иметь в своей основе мел с максимально высоким содержанием СаСО3 с максимально низким содержанием абразивных примесей и в обязательном порядке обработанный стеариновой кислотой. За счет различной кристаллической структуры мела и мрамора меловая добавка на основе мела более предпочтительна, так как она оказывает относительно меньшее абразивное воздействие на оборудование. Кроме основных компонентов меловая добавка может содержать модифицирующие добавки, в частности стеарат цинка, который используется в качестве гидрофобизатора, термостабилизатора и смазывающего вещества.
Также в состав меловой добавки может входить полимерный воск: его содержание может составлять до 4%. Полимерный воск является связующим, необходимым для качественного смешения компонентов добавки (непосредственно мела и полимера) [1]. При использовании сажи в качестве красителя, модификатора электропроводности или УФ-стабилизатора наблюдается прямая зависимость данных свойств от размера частиц, а также от их структурного расположения (рис. 1 и 2) [2].
Таким образом, сам факт обнаружения наполнителя и даже определение его содержания не дает полного понимания о том, какой эффект оказывает именно этот компонент на свойства всей композиции.
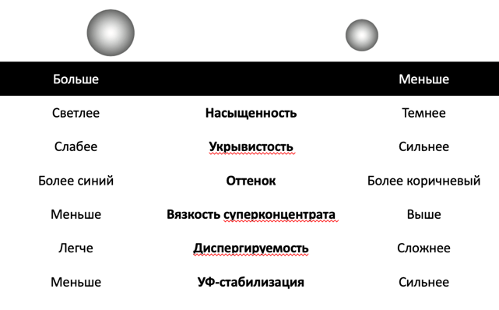
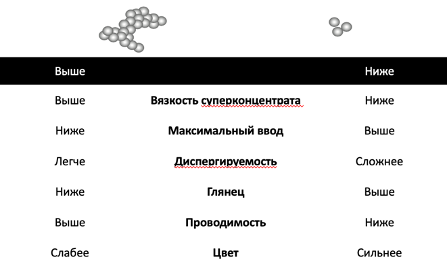
Свойства конечного изделия могут отличаться от паспортных характеристик сырья как в сторону повышения, так и в сторону уменьшения. Большое влияние на такие изменения оказывают технология и параметры производства, наличие добавок, условия и длительность эксплуатации и хранения изделия, по образцу которого проводят реверс-инжиниринг. Без учета этих факторов возникает большая вероятность выбора материала для производства с заниженными характеристиками или с завышенной стоимостью.
Одним из ярких примеров характеристики сырья, при упоре на который происходит некорректный выбор материала, является верхний предел температуры эксплуатации. В паспорте материала могут быть указаны значения таких свойств, как температура размягчения по Вика или температура деформации под нагрузкой (HDT). На практике эти свойства не отражают реальную стойкость готового изделия к нагреву, так как не учитывают такие эффекты, как ползучесть, посткристаллизацию, а также влияние остаточных напряжений.
Другим примером неверной интерпретации является корелляция значения такого относительного показателя, как модуль упругости, характеризующего жесткость, с абсолютным значением усилия, которое необходимо приложить для деформации изделия. При этом не всегда обращается внимание на то, что показатель модуля превышает показатель прочности при разрушении на 2-3 порядка. Такое непонятное, на первый взгляд, соотношение вызвано наличием безразмерных величин в формуле расчета модуля.
Технологические параметры производства — производительность линии, интенсивность охлаждения, метод съема изделий, условия хранения — также оказывают существенное влияние на результат.
2. Cabot Corporation. Application Guide Specialty Carbon Black for Plastics Application Overview. pdf. 2021.